Comprehensive Guide to Plastic Injection Molds: Unleashing Precision and Innovation with Metal Fabricators at DeepMould
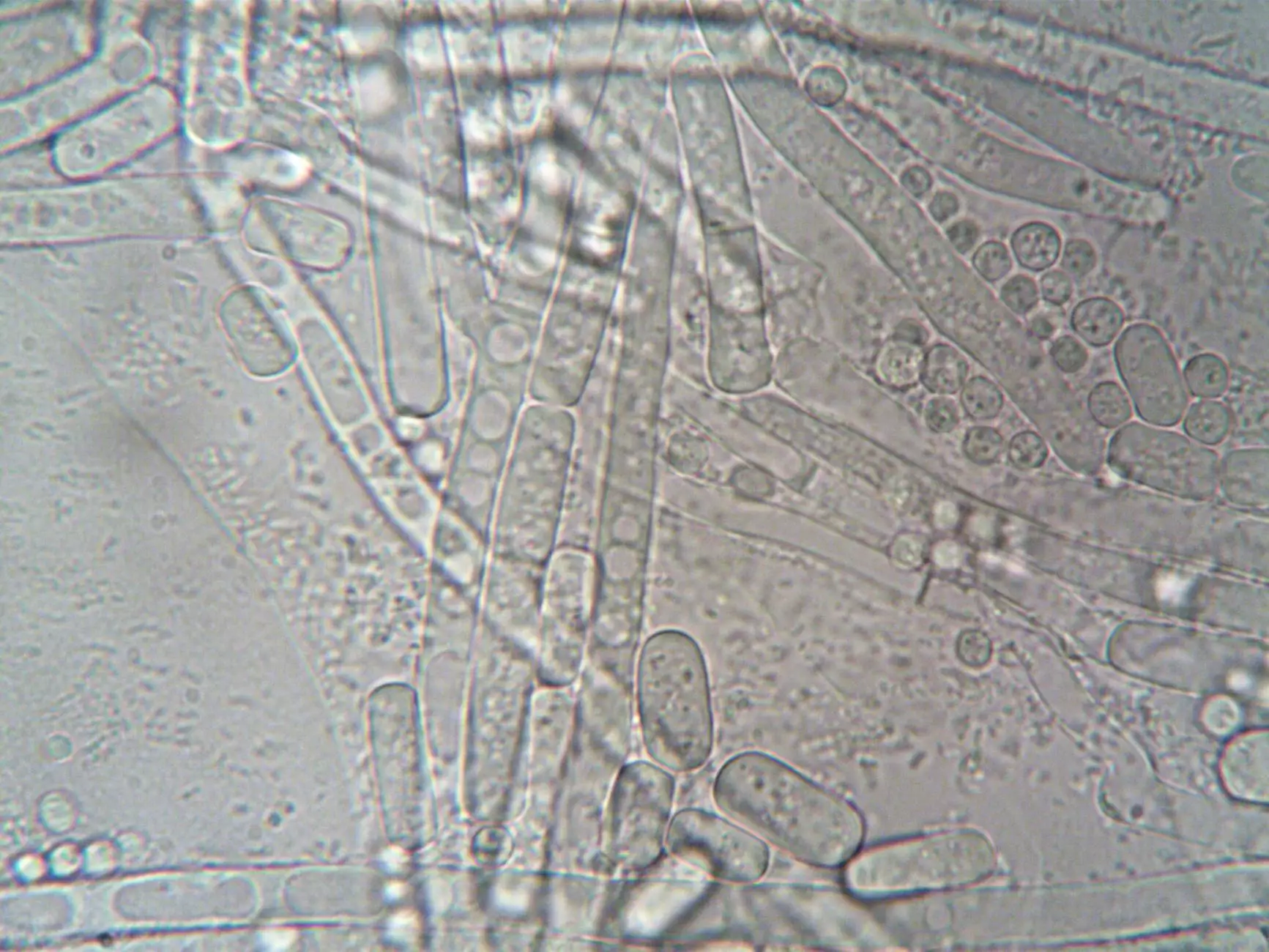
In the ever-evolving landscape of manufacturing and industrial design, plastic injection molds have emerged as a cornerstone technology that drives efficiency, precision, and innovation across diverse sectors. The mastery of creating high-quality, durable, and complex molds is a specialized craft that metal fabricators at DeepMould excel in, leveraging advanced techniques, cutting-edge materials, and meticulous craftsmanship to deliver unrivaled solutions.
Understanding the Role of Plastic Injection Molds in Modern Manufacturing
Plastic injection molds are fundamental tools that facilitate the production of intricate plastic parts with high accuracy and consistency. These molds are essentially custom-designed cavities, sculpted from metallic materials, into which molten plastic is injected under high pressure. Once cooled, the plastic solidifies into the desired shape, ready for assembly or deployment in various products.
From automotive components and consumer electronics to medical devices and household goods, the versatility of plastic injection molding hinges on the quality and precision of the molds used. Therefore, choosing exceptional metal fabricators capable of delivering top-tier plastic injection mold manufacturing is essential for achieving optimal product quality, cost-efficiency, and scalable production.
Why DeepMould’s Metal Fabricators Are Industry Leaders in Plastic Injection Molds
- Unmatched Expertise: DeepMould’s team possesses decades of hands-on experience in designing and fabricating plastic injection molds, ensuring maximum precision and durability in every project.
- State-of-the-Art Technology: Employing CNC machining, electrical discharge machining (EDM), and 3D CAD/CAM software, DeepMould guarantees high-accuracy mold fabrication that meets intricate specifications.
- Material Innovation: The use of premium-grade tool steels such as P20, H13, and stainless steels allows for extensive mold longevity, resistance to wear, and ability to produce complex geometries.
- Customized Solutions: Recognizing that each product has unique requirements, DeepMould offers tailored mold designs that optimize cycle times, reduce defects, and enhance product quality.
- Rigorous Quality Control: Multiple inspection stages, including coordinate measuring machine (CMM) verification, ensure mold precision before delivery.
The Process of High-Quality Plastic Injection Mold Manufacturing at DeepMould
Creating an effective plastic injection mold at DeepMould involves a comprehensive, meticulous process designed to guarantee precision, durability, and efficiency. The process can be broken down into several core phases:
1. Concept and Design
This initial phase involves collaboration with clients to understand product specifications, intended use, and production volume. Using advanced CAD software, engineers develop detailed 3D models and mold designs that account for shrinkage, venting, cooling channels, and ejection systems.
2. Material Selection
Choosing the right high-grade steel or other alloys ensures the mold can withstand repeated cycles, resist wear, and deliver consistent quality. DeepMould’s material specialists evaluate environmental conditions and production demands to recommend optimal materials.
3. Precision Machining
The manufacturing process begins with CNC machining, where computer-controlled equipment carve out the mold halves with micron-level accuracy. Techniques like wire EDM are employed for complex geometries and fine details, critical for high-precision plastic injection molds.
4. Heat Treatment and Finish
Post-machining, molds undergo heat treatment to enhance hardness and wear resistance. Surface finishing processes such as polishing, texturing, and coating are applied to optimize mold surface quality, which directly affects the surface finish of the final plastic parts.
5. Assembly and Testing
Once assembled, the molds are subjected to rigorous testing, including trial runs with actual production samples, to verify dimensional accuracy, ejection functions, cooling efficiency, and cycle times. Adjustments are made as necessary to meet precise specifications.
6. Maintenance and Aftercare
High-quality molds require ongoing maintenance for optimal performance and longevity. DeepMould provides comprehensive after-sales services, including prompt repairs, component replacements, and preventive maintenance planning.
Innovations in Plastic Injection Molds: Pushing the Boundaries with DeepMould
The industry continually evolves, driven by innovations that open new possibilities for product design and manufacturing. DeepMould stays ahead of the curve by integrating the latest advancements such as:
- Rapid Prototyping for early-stage validation, reducing development time and costs.
- Advanced Cooling Technologies such as conformal cooling channels, which significantly decrease cycle times and improve part quality.
- Multi-Cavity Molds for high-volume production, boosting efficiency without compromising precision.
- Hot Runner Systems to eliminate sprue marks, minimize waste, and ensure uniform melt flow.
- Electroforming and Surface Treatments that lend aesthetic qualities and functional enhancements to molds.
The Impact of High-Quality Plastic Injection Molds on Product Development and Business Success
Leveraging premium plastic injection molds from trusted metal fabricators like DeepMould leads to tangible benefits, empowering businesses to thrive in competitive markets:
- Enhanced Product Quality: Precisely manufactured molds produce consistent, defect-free parts with superior surface finishes, bolstering brand image and customer satisfaction.
- Reduced Production Costs: Efficient mold designs and optimized cooling channels minimize cycle times and material waste, increasing profitability.
- Faster Time-to-Market: Advanced manufacturing processes shorten development cycles, enabling rapid deployment of new products.
- Design Flexibility: Complex geometries and integrated features are achievable, inspiring innovative product concepts.
- Sustainability: Durable molds reduce downtime and waste, aligning with environmentally responsible manufacturing practices.
Choosing the Right Metal Fabricator for Your Plastic Injection Mold Needs
Quality is paramount when selecting a metal fabricator for plastic injection molds. Factors to consider include:
- Experience and Reputation: Proven track record in mold manufacturing and positive client testimonials.
- Technical Capabilities: Access to advanced machinery, design software, and materials.
- Customization and Flexibility: Willingness to tailor solutions based on specific project requirements.
- Quality Assurance: Rigorous inspection protocols and certifications such as ISO 9001.
- After-Sales Support: Comprehensive maintenance services and technical support post-production.
DeepMould: Your Partner in High-Performance Plastic Injection Molds
At DeepMould, we understand that plastic injection mold manufacturing is both an art and a science. Our dedication to excellence ensures that every mold we produce meets the highest standards of precision, durability, and efficiency. Our team collaborates closely with clients from concept to production, offering technical expertise and innovative solutions at every stage.
We integrate cutting-edge technologies, sustainable practices, and rigorous quality control to deliver molds that empower your manufacturing processes, reduce costs, and accelerate your growth. Whether you need a prototype mold or high-volume production tooling, DeepMould is your trusted partner for exceptional plastic injection molds.
Conclusion: Elevate Your Manufacturing with Superior Plastic Injection Molds from DeepMould
In today’s highly competitive market, the quality and precision of your plastic injection molds can make all the difference. Partnering with experienced metal fabricators like DeepMould guarantees access to world-class manufacturing capabilities, innovative techniques, and comprehensive support that turn your product visions into reality.
Invest in plastic injection molds that not only meet your current production needs but also elevate your business to new levels of success. With DeepMould’s expertise, advanced technology, and unwavering commitment to quality, your manufacturing future is assuredly bright.
Contact us today to explore how our plastic injection mold solutions can transform your manufacturing process and bring your innovative products to life with exceptional precision and efficiency.