The Essential Role of a **Precision Mold Manufacturer** in Metal Fabrication
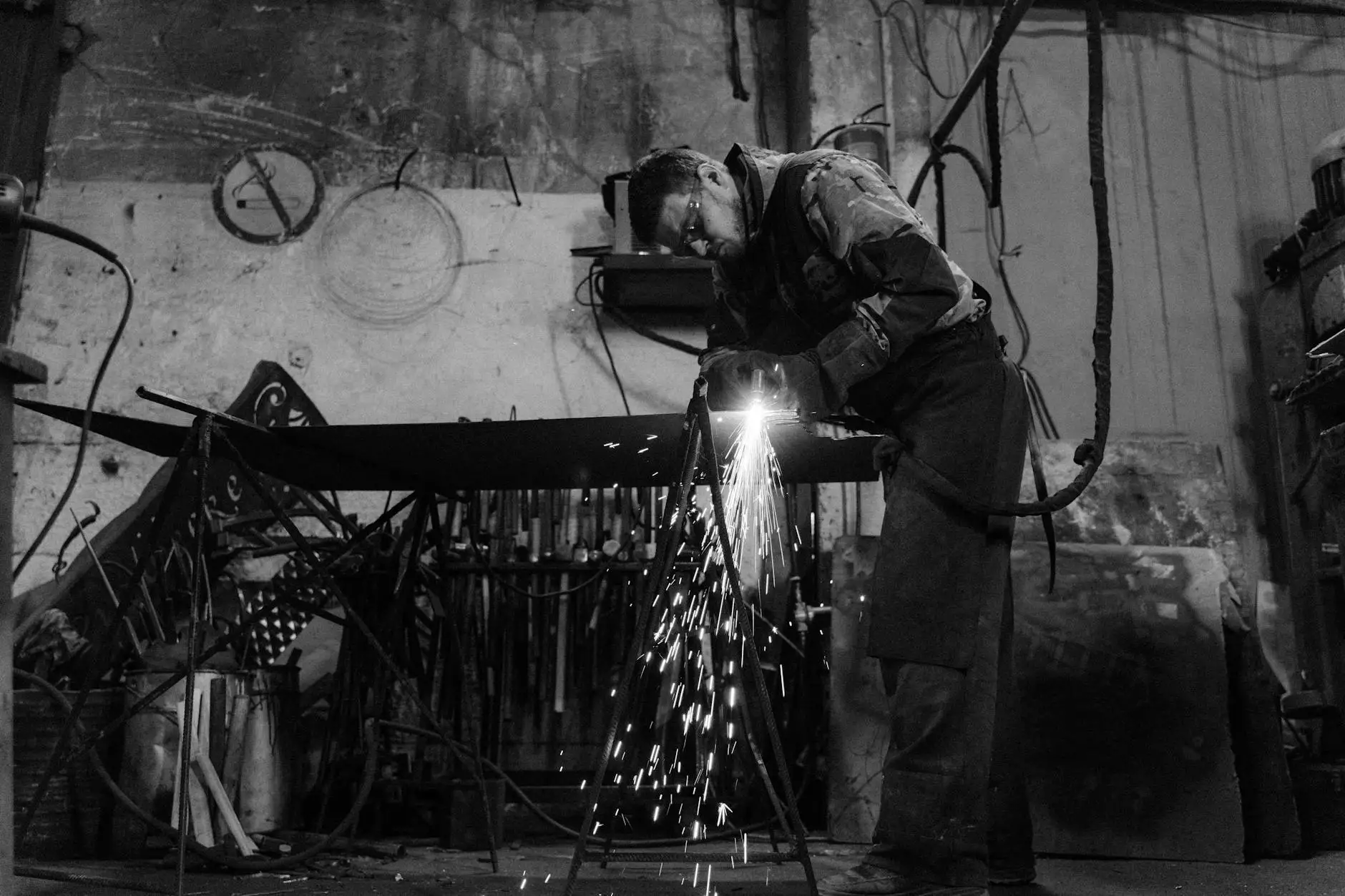
In the world of manufacturing, especially in the metal fabrication sector, the term precision mold manufacturer resonates with significance. Molds are foundational components in producing high-quality products, particularly in industries ranging from automotive to consumer goods. At Deepmould.net, we recognize the critical aspects that make our services stand out in this competitive landscape.
The Foundation of Precision: What Makes a Mold Manufacturer Stand Out?
To grasp why Deepmould.net is a leading precision mold manufacturer, we must first identify what precision means in this context. Precision in manufacturing involves not just the dimensional accuracy of the mold but also consistency and repeatability in production. Here are key attributes that distinguish an exceptional mold manufacturer:
- Advanced Technology: Using state-of-the-art machinery and software can significantly enhance the precision and efficiency of mold fabrication.
- Expertise and Experience: Team members who are skilled and seasoned in mold design and manufacturing often lead to better outcomes.
- Quality Assurance: Implementing thorough inspection processes ensures that every mold meets strict industry standards.
- Material Selection: The right materials contribute to the longevity and effectiveness of molds, impacting overall product quality.
- Customization Capabilities: The ability to create tailored molds to meet specific client needs is crucial for maintaining competitive advantages.
The Precision Mold Manufacturing Process
The process of manufacturing molds at Deepmould.net is intricate and methodical. Here’s a step-by-step guide to how we ensure excellence in our output:
1. Consultation and Design
Every successful project begins with a thorough consultation. Our team collaborates with clients to understand their unique needs and specifications. Using advanced CAD software, we design molds that adhere to the precise parameters required for production.
2. Material Selection
Choosing the right material is crucial. Molds can be made from various materials, including steel, aluminum, and specialty composites. Each material is selected based on the intended application, durability required, and budget constraints.
3. Machining
The machining process involves using CNC (Computer Numerical Control) machines to carve out the precise shapes and features of the molds. Our fleet of advanced machines ensures that tolerances are held tightly, which is critical for high-precision applications.
4. Surface Treatment
After machining, molds may undergo various surface treatments to enhance their performance, including heat treatment to increase hardness and anodizing or plating for corrosion resistance.
5. Quality Control
Once fabrication is complete, each mold undergoes rigorous quality control checks. This phase ensures that every mold meets the quality standards required before they leave our facility.
6. Testing and Validation
Before mass production begins, molds are tested to validate their performance. This step ensures that they produce components that meet all specifications consistently.
The Importance of Quality in Precision Molds
In the realm of manufacturing, quality is paramount. For a precision mold manufacturer like Deepmould.net, delivering high-quality molds impacts not only our reputation but also that of our clients. Molds that are not constructed to rigorous standards can lead to:
- Increased production costs due to rework and scrap.
- Delays in time-to-market for end products.
- Decreased customer satisfaction stemming from product defects.
- Financial losses from wasted materials.
By investing in quality at every stage, we ensure that our clients receive the most reliable and efficient molds available.
Innovations in Mold Manufacturing
The landscape of manufacturing is continually evolving, and innovations play a crucial role in shaping the future of precision mold manufacturing. Deepmould.net stays at the forefront of these advancements, incorporating technologies such as:
- 3D Printing: For rapid prototyping and complex geometries that traditional machining cannot easily achieve.
- IoT Integration: Utilizing smart technology to monitor molds and machinery in real-time for improved efficiency and maintenance.
- CAM Software: Enhancing the production process by optimizing cutting paths and tool usage, leading to shorter manufacturing cycles.
Sustainability in Mold Manufacturing
As global awareness of environmental issues rises, Deepmould.net is committed to sustainable practices in mold manufacturing. By incorporating eco-friendly materials and reducing waste through efficient machining strategies, we strive to minimize our ecological footprint while maintaining superior quality standards.
Benefits of Sustainable Practices
Opting for greener manufacturing processes brings not only environmental benefits but also advantages for businesses:
- Cost Savings: Efficient resource use leads to lower operational costs.
- Enhanced Brand Image: Companies that prioritize sustainability are often preferred by customers.
- Regulatory Compliance: Staying ahead of regulations helps mitigate risks related to environmental legislation.
Industry Applications of Precision Molds
Precision molds manufactured by Deepmould.net serve a broad array of industries, showcasing our ability to cater to diverse needs. Here are some key sectors that benefit significantly from our molds:
Aerospace
The aerospace industry demands uncompromising precision due to safety standards. Our molds support the production of components that are critical to aircraft performance and safety.
Automotive
In the automotive sector, our molds are essential for producing everything from engine parts to dashboard components, where precision translates directly into performance and safety.
Consumer Electronics
Precision molds help in creating intricate, high-tech products that consumers demand now more than ever, supporting everything from smartphones to smart home devices.
Medical Devices
This industry requires molds that meet strict regulatory standards. Our precision manufacturing allows for the creation of life-saving medical products that are safe and reliable.
Choosing the Right Precision Mold Manufacturer
Selecting a precision mold manufacturer is a significant decision that affects production efficiency and product quality. Here are several factors to consider when choosing a partner:
- Reputation: Research the manufacturer's track record; look for testimonials and case studies that demonstrate their capabilities.
- Technology and Innovation: Ensure they invest in modern technology and continuously improve their processes.
- Customer Service: Effective communication and support throughout the manufacturing process are essential.
- Scalability: Choose a manufacturer capable of scaling production to meet your growing needs without sacrificing quality.
Conclusion: The Future of Precision Mold Manufacturing
The role of a precision mold manufacturer extends beyond mere production; it encompasses innovation, quality assurance, and a commitment to sustainable practices. At Deepmould.net, we pride ourselves on being at the forefront of the mold manufacturing industry, consistently integrating the latest advancements and focusing on customer satisfaction.
As we look to the future, staying agile and adapting to industry changes will be crucial. A focus on precision, quality, and sustainability will guide us in meeting our clients' evolving needs. Join us as we continue to lead the charge in precision mold manufacturing and deliver exceptional value to businesses across various sectors.