The Rising Influence of Plastic Injection Molding Factory in Today’s Economy
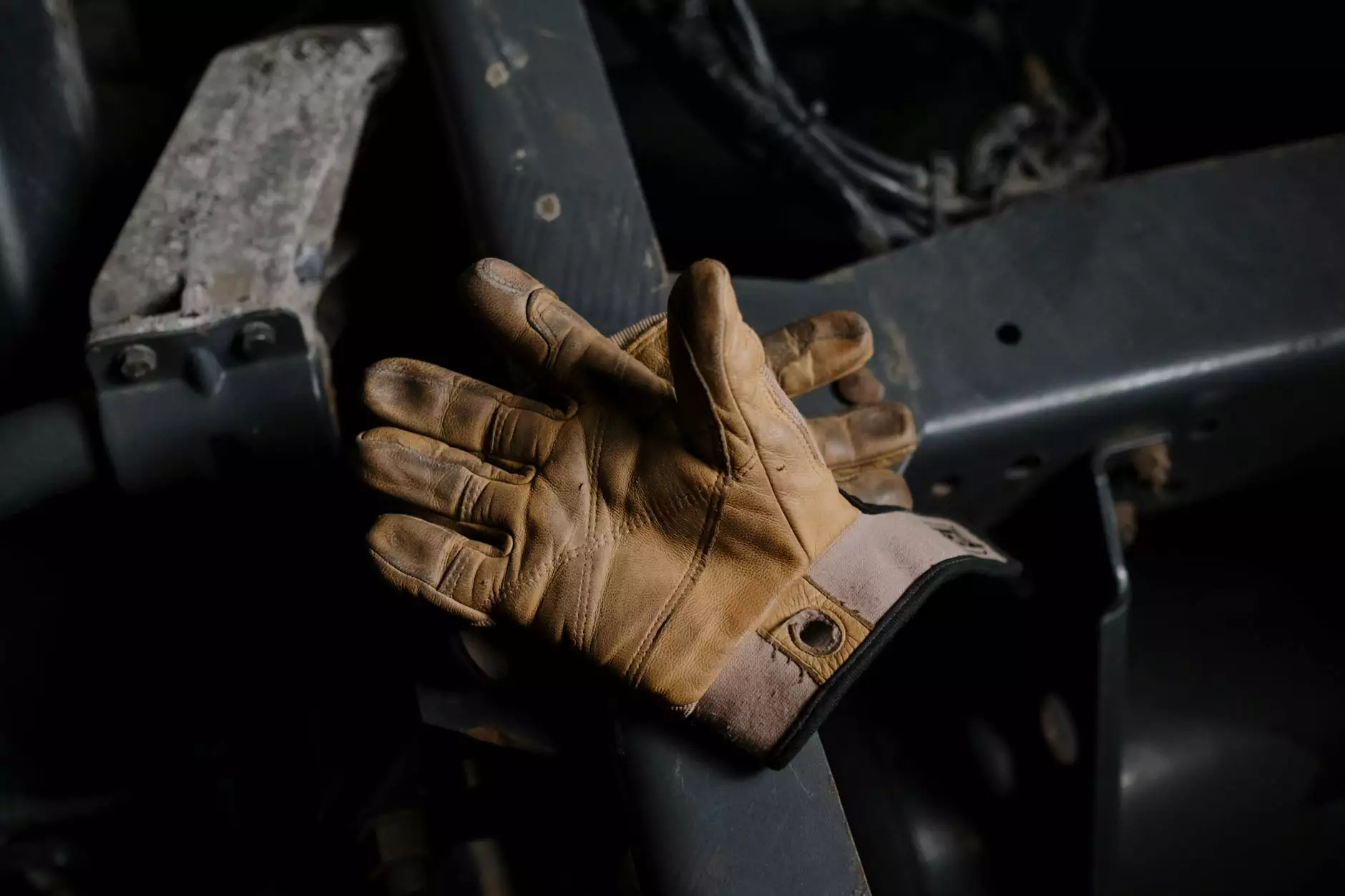
In the rapidly evolving world of manufacturing, the plastic injection molding factory stands out as a pinnacle of efficiency and precision. This article explores the critical role of plastic injection molding in various industries, the complex processes involved, and the immense benefits these factories bring to the business landscape.
Understanding Plastic Injection Molding
To appreciate the impact of a plastic injection molding factory, it is essential first to understand what plastic injection molding is. This sophisticated manufacturing process involves injecting molten plastic into a mold to create various products. The pressure and heat applied during this process allow for the detailed and intricate designs that are crucial in today’s market.
How Does Plastic Injection Molding Work?
The operation of a plastic injection molding factory involves several key stages:
- Material Preparation: The process begins with the selection and preparation of plastic materials, typically in pellet form. These materials are carefully chosen based on the properties required for the final product.
- Injection: The prepared pellets are heated until melted and then injected into a pre-designed mold under high pressure.
- Cooling: Once injected, the molten plastic cools and solidifies in the mold, taking the shape of the designed product.
- Demolding: After cooling, the mold is opened, and the new plastic component is removed.
- Finishing: The last stage often involves additional processes such as trimming, painting, or assembling, to ensure that the product meets quality standards.
Why Choose a Plastic Injection Molding Factory?
The advantages of working with a plastic injection molding factory are manifold. Companies across different sectors benefit from this method due to its efficiency, scalability, and versatility.
1. Cost Efficiency
One of the primary reasons businesses opt for plastic injection molding is cost efficiency. Once the molds are created, the cost of manufacturing each piece decreases significantly, making it an economical choice for large production runs.
2. High Precision and Quality
Plastic injection molding provides unparalleled precision. This accuracy is crucial in industries such as automotive and medical, where precision components are not just preferred but required for safety and functionality.
3. Versatility in Design
Another benefit is the versatility in design. With a plastic injection molding factory, complex designs and intricate details are achievable. This capability allows companies to innovate and bring their visions to life without the constraints often found in other manufacturing processes.
4. Fast Production Rate
Speed is of the essence in today’s market, and plastic injection molding is known for its rapid production rate. The process allows for quick turnaround times, helping companies meet tight deadlines and respond to market demands swiftly.
Applications of Plastic Injection Molding
The application of plastic injection molding spans across numerous industries, demonstrating its wide-ranging impact. Here are some of the key sectors benefitting from this manufacturing process:
- Automotive Industry: From dashboard components to under-the-hood parts, plastic injection molding plays a vital role in producing lightweight and durable automotive components.
- Consumer Goods: Many everyday products, including toys, appliances, and packaging, are produced using this method, showcasing the versatility of plastic molding.
- Medical Devices: Precision medical parts must meet strict international quality standards, making injection molding ideal for creating reliable, clean, and safe medical devices and components.
- Electronics: The housing of electronic devices often involves molded plastic parts that are cost-effective and can be produced quickly with high precision.
- Building and Construction: Components such as pipes, fittings, and fixtures are often manufactured through this process, emphasizing the strength and reliability of molded plastics in construction.
Sustainability in Plastic Injection Molding
In recent years, sustainability has become a paramount concern for manufacturers globally. The good news is that plastic injection molding factories are evolving to support sustainable practices.
1. Use of Recycled Materials
Many factories are now integrating recycled plastics into their production processes, which significantly reduces waste and environmental impact.
2. Energy Efficiency
Modern molding machines are designed to consume less energy, thus reducing the carbon footprint of the production process.
3. Reduced Waste Generation
With precise molding capabilities, there’s less material waste compared to traditional manufacturing processes, making it a more environmentally friendly option.
Challenges Faced by Plastic Injection Molding Factories
While the benefits of plastic injection molding are considerable, there are challenges that factories must navigate to maintain efficiency and quality.
1. Initial Investment Costs
Setting up a plastic injection molding factory requires significant capital investment. High-quality molds can be expensive and must be carefully designed and tested.
2. Maintenance of Equipment
Regular maintenance of machines is crucial to ensure consistent production quality. Neglecting maintenance can lead to defects and increased downtime.
3. Skilled Labor Shortages
There is a continual need for skilled laborers who can operate complex machinery and troubleshoot issues as they arise. Factories that fail to invest in training may struggle with production efficiency.
Future Trends in Plastic Injection Molding
The future of plastic injection molding is bright, with several emerging trends poised to shape its evolution. The following innovations and trends will likely play a significant role:
1. Advanced Technologies
Technologies such as artificial intelligence and automation are increasingly being integrated into the molding process. These innovations enhance predictive maintenance and streamline overall production.
2. Bioplastics
The rise of environmentally friendly materials, such as bioplastics, presents exciting opportunities for plastic injection molding factories to contribute further to sustainability efforts.
3. Smart Manufacturing
Integrating IoT (Internet of Things) technologies could revolutionize monitoring and managing production processes, ensuring that any anomalies are detected and resolved promptly.
Conclusion: The Strategic Importance of Plastic Injection Molding Factories
As we delve deeper into the 21st century, the role of the plastic injection molding factory cannot be overstated. Its ability to provide cost-effective, high-precision, and rapidly produced components makes it invaluable in various industries. Furthermore, with a growing emphasis on sustainability and technological advancement, these factories are set to become even more integral to the future of manufacturing.
At DeepMould.net, we understand the critical significance of quality in molding processes and the importance of staying ahead with trends in technology and sustainability. Investing in a plastic injection molding factory is not merely a business decision; it’s a step towards shaping a more efficient and sustainable future in manufacturing.