Unveiling the World of Plastic Molding Manufacturers
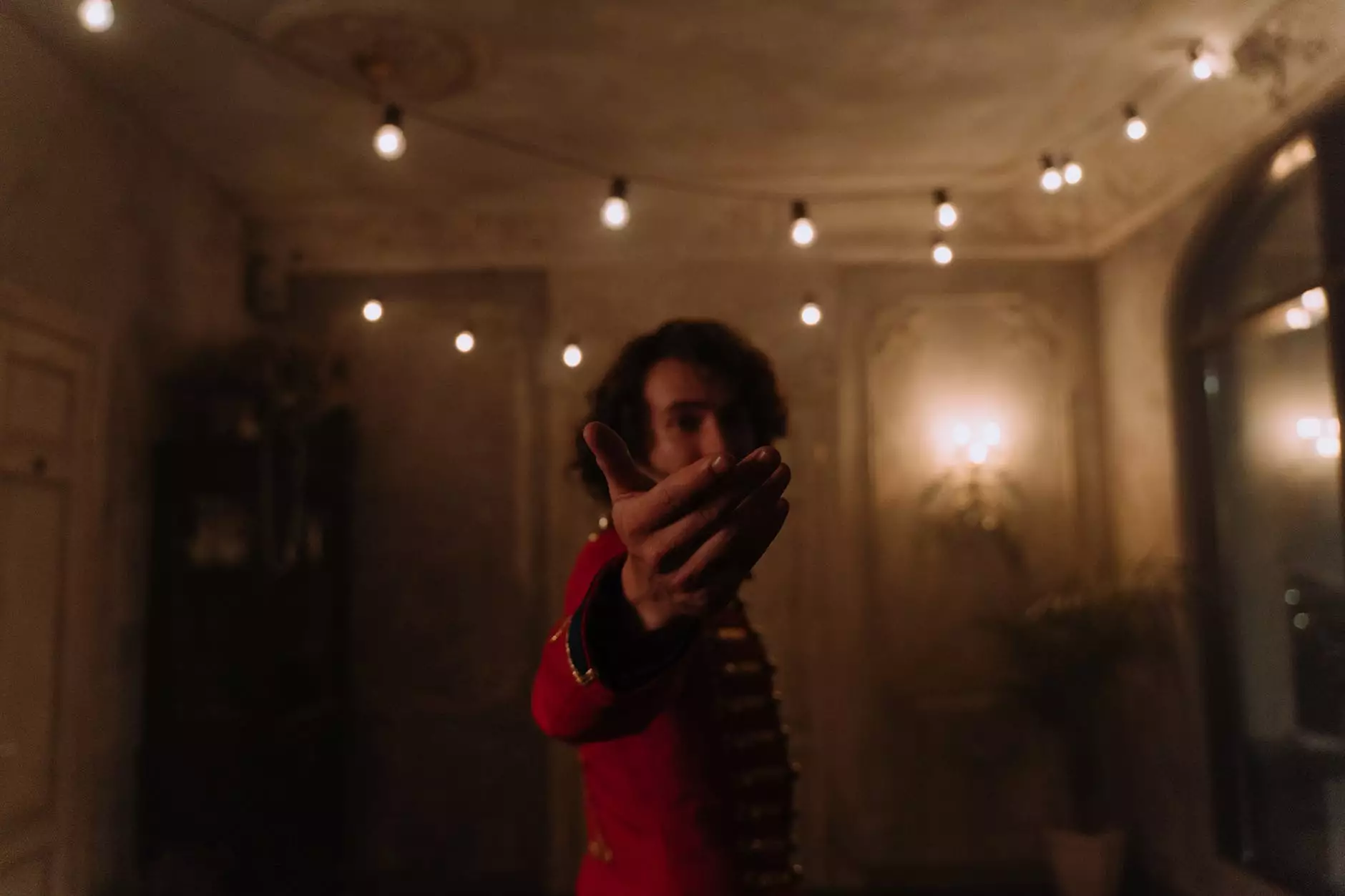
In contemporary manufacturing, the significance of plastic molding cannot be overstated. As one of the most versatile and efficient methods of producing components, plastic molding has captured a substantial sector of global industry practices. This article delves deep into the realm of plastic molding manufacturers, focusing on the intricacies of production processes, benefits, and innovations within the field, particularly highlighting our expertise at Hanking Mould.
Understanding Plastic Molding
Plastic molding is a manufacturing process for producing parts by injecting molten material into a mold. This process allows manufacturers to create plastic parts in various shapes, sizes, and designs, making it indispensable in numerous applications. The primary types of plastic molding include:
- Injection Molding
- Blow Molding
- Rotational Molding
- Compression Molding
- Thermoforming
The Role of Plastic Mold Makers
Plastic mold makers are crucial in the production chain, as they design and manufacture the molds used in various molding processes. High-quality molds are vital for ensuring that produced parts meet precise specifications and standards. At Hanking Mould, we pride ourselves on our ability to deliver exceptional mold-making solutions that meet the rigorous demands of our clients.
The Significance of Quality in Mold Making
Quality is paramount in the mold-making process. The precision of a mold directly affects the quality of the end product. Here are some of the key quality aspects to consider:
- Material Choice: The selection of high-grade materials ensures durability and the ability to withstand high temperatures during the injection process.
- Precision Engineering: Modern CNC machining techniques contribute to the accuracy needed in mold fabrication.
- Surface Finishing: The surface finish of molds influences the quality of part finish. A smooth mold surface results in a better product appearance.
Injection Mould Manufacturer: A Specialized Sector
The role of an injection mould manufacturer is specific and critical. This process involves numerous steps, from the conceptual design of the mold to the final production run of plastic parts. Companies like Hanking Mould utilize cutting-edge technology and methods to ensure efficiency and accuracy at every step. Here’s how the injection molding process typically unfolds:
The Injection Molding Process
The injection molding process can be summarized in the following steps:
- Material Preparation: Raw plastic materials, usually in the form of pellets, are fed into the injection machine.
- Heating and Melting: The pellets are heated until they become a molten state, allowing for easy flow into the mold.
- Injection: The molten plastic is injected under high pressure into a closed mold.
- Cooling: The plastic cools and solidifies within the mold cavity.
- Mold Opening and Part Ejection: The mold opens, and the finished part is ejected.
Key Advantages of Working with Plastic Molding Manufacturers
Partnering with reputable plastic molding manufacturers is integral for businesses seeking quality and efficiency. The advantages include:
- Cost Efficiency: Optimized production processes significantly reduce manufacturing costs.
- Scalability: These manufacturers provide solutions that can easily scale part production up or down based on market demands.
- Design Flexibility: Advanced design options allow for modifications during production, accommodating changes and innovations.
Innovations in Plastic Molding Technologies
The world of plastic molding is continuously evolving. Innovations in technology enhance the efficiency and precision of manufacturing processes. Some key advancements include:
1. 3D Printing Integration
The integration of 3D printing technology allows for rapid prototyping and mold development. This adaptation speeds up the design phase and enables manufacturers to test and validate new product designs efficiently.
2. Smart Manufacturing Technologies
With the emergence of the Internet of Things (IoT) and Industry 4.0 practices, manufacturers are leveraging smart technologies. This transition is leading to predictive maintenance, enhanced productivity, and stringent quality control.
3. Sustainable Practices
As environmental concerns grow, many plastic molding manufacturers are adopting sustainable practices. This includes using recycled materials and developing biodegradable plastics to minimize environmental impact.
Choosing the Right Plastic Molding Manufacturer: Key Considerations
When selecting a plastic molding manufacturer, several factors should guide your decision. Here are vital considerations:
- Experience and Expertise: A manufacturer with a proven track record often signifies reliability and quality.
- Technology and Equipment: Ensure the manufacturer uses advanced technology and well-maintained equipment to produce high-quality products.
- Customer Support: A responsive customer service team is invaluable for addressing queries and potential issues.
- Testimonial and Reputation: Look for reviews, case studies, and testimonials from previous clients that reflect the manufacturer's standing in the industry.
Conclusion: The Future of Plastic Molding Manufacturing
As industries evolve and technology advances, the future of plastic molding manufacturers looks brighter than ever. The push towards sustainable manufacturing, coupled with technological advancements, is shaping a dynamic landscape where quality, efficiency, and adaptability are paramount. At Hanking Mould, we stand at the forefront of this evolution, dedicated to delivering innovative and high-quality plastic solutions to our clients.
Embarking on a journey with experienced and forward-thinking manufacturers like us can lead to significant advantages for your business. Connect with Hanking Mould today to discover how we can transform your plastic molding needs into exceptional products.